W nowoczesnej produkcji elektroniki, gdzie dominują obwody w nanoskali i wrażliwe komponenty, wyładowania elektrostatyczne (ESD) stanowią poważne zagrożenie. Często niewykrywalne dla ludzi, ale niszczące na poziomie mikroelektronicznym, ESD zagraża niezawodności urządzenia, zwiększa koszty produkcji i niszczy wiarygodność marki. W miarę jak komponenty zmniejszają się poniżej 5 nm, a urządzenia IoT rozwijają się, branża staje w obliczu paradoksu: podczas gdy miniaturyzacja napędza innowacje, wykładniczo zwiększa również podatność na ESD.
Co oznacza skrót ESD w kontroli procesu?
Od Podstawowa wiedza na temat ESDWiemy, w jaki sposób generowane są wyładowania elektrostatyczne. Podczas gdy elektryczność statyczna może wydawać się nieszkodliwa w codziennym życiu, jej konsekwencje przemysłowe są znacznie poważniejsze. Choć niewykrywalne dla ludzkich zmysłów, ESD stanowi krytyczne zagrożenie w produkcji elektroniki. Pojedyncze wyładowanie elektrostatyczne może natychmiast zniszczyć komponenty lub stworzyć ukryte wady, które omijają standardowe kontrole jakości. Te ukryte wady często ujawniają się później jako niewyjaśnione awarie w terenie, prowadząc do kosztownych roszczeń gwarancyjnych, zagrożeń dla bezpieczeństwa i trwałego uszczerbku na reputacji marki.
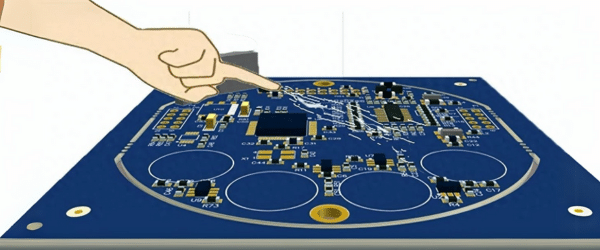
W rezultacie, kompleksowe Program kontroli ESDm-w tym systemy jonizacji, Obszar kontroli ESDkontrola wilgotności i training dla empracownicy i nie tylko - mają kluczowe znaczenie dla zapewnienia niezawodności produktów elektronicznych.
Dwa tryby awarii komponentów elektronicznych spowodowane przez ESD
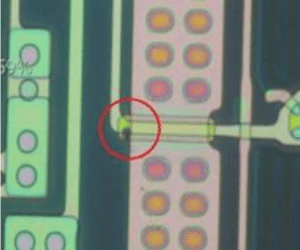
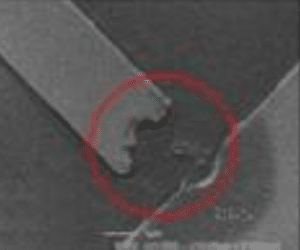
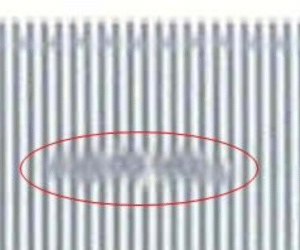
1. Katastrofalna awaria
- Całkowita utrata funkcjonalności z powodu poważnego pogorszenia parametrów elektrycznych
- Reprezentuje ~10% awarii komponentów spowodowanych ESD
2. Wady ukryte
- Komponenty początkowo spełniają specyfikacje, ale okazują się wadliwe:
- Znacznie skrócona żywotność operacyjna
- Naruszona niezawodność
- Potencjał nagłej awarii pod wpływem późniejszych naprężeń
- Odpowiada za ~90% uszkodzeń związanych z ESD
Ten tryb ukrytej awarii stwarza większe ryzyko, ponieważ zagrożone komponenty mogą przejść wstępne kontrole jakości, ale powodować awarie w produktach końcowych.
Mechanizmy uszkodzeń wywołanych wyładowaniami elektrostatycznymi w produkcji elektroniki
- Niewspółosiowość podczas montażu
Pola statyczne mogą przemieszczać mikrokomponenty podczas umieszczania, powodując tombstoning lub słabe połączenia lutowane, które mogą zostać wykryte dopiero w późniejszych fazach testowania. - Nagromadzenie ładunku w sprzęcie
Części przewodzące maszyn SMT gromadzą ładunki elektrostatyczne, grożąc ukrytym uszkodzeniem półprzewodników, jeśli nie zostaną zneutralizowane poprzez uziemienie lub jonizację. - Przyspieszenie zanieczyszczenia
Naładowane powierzchnie przyciągają kurz 100 razy szybciej, tworząc ścieżki przewodzące, które powodują zwarcia lub zakłócenia sygnału. - Adhezja składników pasożytniczych
Ładunki elektrostatyczne powodują, że części przywierają do opakowań lub narzędzi, ryzykując uszkodzenia fizyczne i ładunki resztkowe, które zniekształcają wyniki testów.
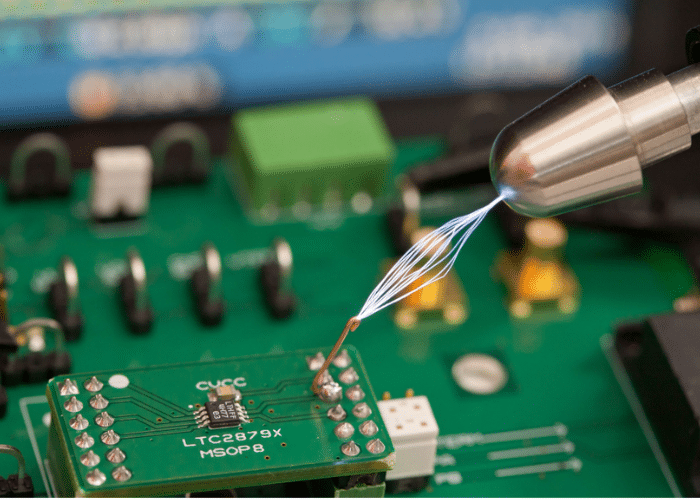
Incydenty związane z wyładowaniami elektrostatycznymi w produkcji elektroniki
Według szacunków ESD powoduje od $5 do $9 miliardów rocznych strat w globalnym przemyśle produkcji elektroniki. Raport ESDA z 2021 r.. Straty te wynikają z uszkodzonych komponentów, opóźnień w produkcji i kosztownych wycofań. Poniżej znajdują się godne uwagi rzeczywiste incydenty podkreślające poważne skutki finansowe i operacyjne ESD
1. Awarie procesorów AMD (1994)
Firma: Advanced Micro Devices (AMD)
Incydent: Wyładowania elektrostatyczne podczas obsługi uszkodziły tysiące procesorów K5 podczas produkcji, powodując ukryte wady i awarie w terenie.
Strata: Szacowany koszt wymiany $12M i szkody dla reputacji.
Źródło: Studium przypadku stowarzyszenia ESD
2. Automotive ECU Recall (2018)
Firma: Główny europejski producent samochodów
Incydent: Wyładowania elektrostatyczne podczas montażu uszkodziły oprogramowanie układowe w 150 000 jednostek sterujących silnika (ECU), powodując losowe wyłączenia.
Strata: $47M w związku z wycofaniem i wstrzymaniem produkcji.
Źródło: Raport branżowy sporządzony przez audytorów IATF 16949 (Strona 22).
3. Awarie ekranu dotykowego Tesla Model 3 (2020)
Firma: Tesla
Incydent: Wrażliwe na wyładowania elektrostatyczne komponenty ekranu dotykowego uległy przedwczesnej degradacji z powodu niewystarczającego uziemienia fabrycznego.
Strata: $135M (kampania NHTSA 21V035000).
Źródło: Raport NHTSA o wycofaniu produktu z rynku (Wyszukaj "21V035000").