In the article, Basic knowledge of ESD, we discussed the basics of electrostatic charge and discharge, the mechanisms of electrostatic generation, ESD events, and ESD damage. To safeguard products against damage caused by electrostatic discharge (ESD), the implementation of a comprehensive ESD control program is essential.
Fundamental Principles of ESD Control
Before developing the ESD control program, it is crucial to understand fundamental principles of ESD control.
1. Design Protection
The first fundamental principle focuses on developing products and assemblies that can reasonably withstand the effects of ESD. This includes using low-ESD-sensitive components whenever possible and incorporating input protection mechanisms such as ESD protection circuits and filters.
2. Define ESD Protected Areas
Marking specific zones as ESD protected helps restrict access to authorized personnel only. By implementing an ESD access control system, the potential for ESD incidents is effectively managed. These areas should be equipped with essential ESD control tools, including anti-static flooring, workbenches, and storage cabinets, to ensure that all operations conducted within these zones adhere to ESD control standards, thereby minimizing the risk of electrostatic discharge.
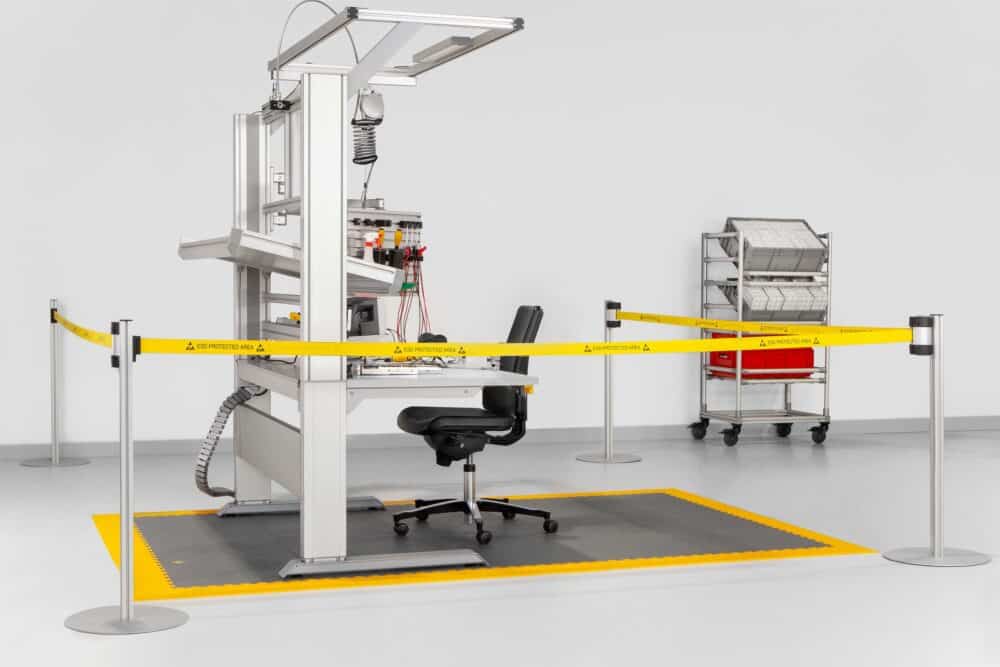
3. Determine Control Levels for ESD Protected Areas
For extremely sensitive components, stricter control measures may be necessary, including enhanced grounding protocols and environmental monitoring. This requires a comprehensive evaluation of the device’s static sensitivity, the materials in use, and the conditions present in the facility to ensure that adequate preventive measures are in place.
4. Minimize Charge Generation
Minimize static charge generation can be achieved through the careful selection of materials and the reduction of friction during handling. For instance, reducing friction between plastics and other surfaces, as well as utilizing conductive or antistatic materials, can decrease the likelihood of static charge accumulation. Additionally, arranging equipment effectively and avoiding unnecessary contact further contributes to the reduction of charge generation.
5. Dissipate Static Charges Promptly
An effective grounding system should be instituted within the workspace to facilitate the timely release of static electricity. All equipment and workstations must be thoroughly connected to a common ground to ensure that electrostatic charges are safely discharged. Furthermore, employing ionizers can help neutralize static charges on certain materials without grounding, allowing for safe handling.
6. Shield Against Static
The implementation of shielding techniques serves as a final crucial principle, creating physical barriers that reduce the impact of static electricity on sensitive devices. This can be accomplished through the use of metallic shielding materials, conductive coatings, or specialized packaging materials that effectively prevent or minimize the electric field, thereby protecting components from ESD. When transporting and storing sensitive devices, utilizing ESD protective packaging such as anti-static bags or conductive foam can provide effective defense against electrostatic discharge damage.
Setup an Effective ESD Control Program
An effective ESD control program should encompass two primary aspects: a written ESD control plan and technical requirements.
Written ESD Control Plan
A written ESD control plan serves as an essential document for internally executing ESD control regulations and requirements within an organization. It not only provides employees with clear guidelines for implementation but also ensures that the entire organization recognizes and upholds the importance of ESD control. A complete written ESD control plan typically includes the following three components:
- Personnel Training:
All personnel who work in ESD Protected Areas or handle ESD-sensitive (ESDS) devices must undergo ESD training. The training content should cover fundamental knowledge of static electricity, the impact of ESD on products, and the proper use of ESD protective tools and equipment. The training program should clearly specify the methods and frequency of training and also require that records of the training are maintained. - Product Qualification:
Product qualification involves evaluating selected ESD control materials and equipment including ESD wrist straps, garments, work surfaces, footwear, flooring, etc, according to recognized testing methods and specified limits.
For instance, under the ANSI/ESD S20.20 2021 standard, footwear is tested with ANSI/ESD STM9.1, while work surfaces are evaluated with ANSI/ESD STM4.1.1. Similarly, according to the IEC 61340-5-1 standard, footwear is tested with IEC 61340-4-3c., and work surfaces are assessed with IEC61340-2-3. - Compliance Verification:
Compliance verification is crucial for ensuring the effectiveness of the ESD control program. This typically involves regular inspections and audits to confirm that the procedures are fully implemented. Compliance verification also includes documenting and analyzing failure data to continuously improve ESD control measures and processes.
Technical Requirements
In addition to a written plan, implementing an effective ESD control program also requires meeting certain technical requirements. These requirements typically encompass the following six aspects:
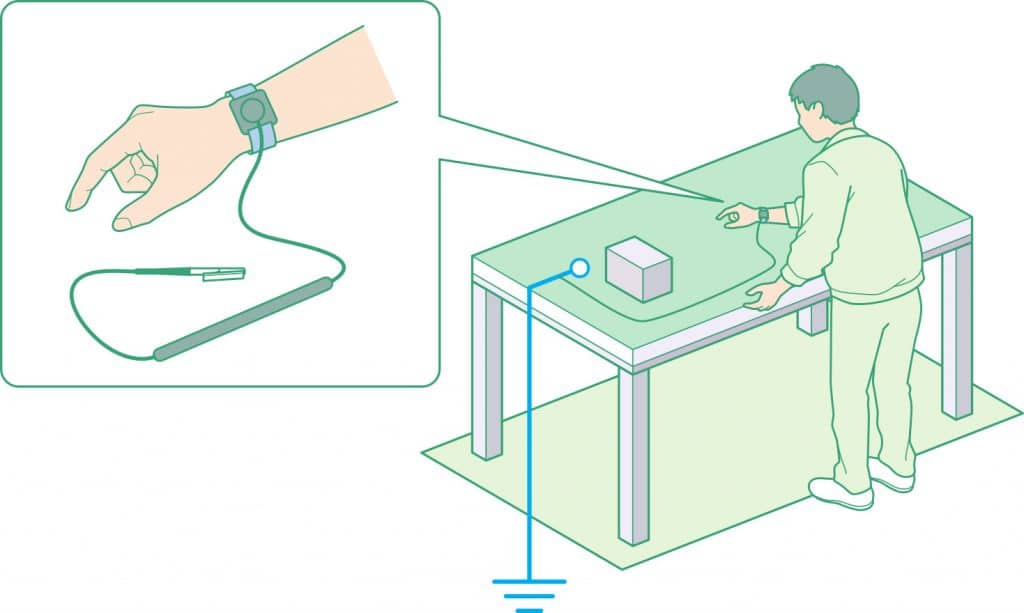
- Grounding/Equal Potential Bonding:
By grounding equipment, tools, and work surfaces, a low-impedance circuit is formed to quickly direct electrostatic charges to the ground, effectively reducing the risk of electrostatic discharge. - Personnel Grounding:
Personnel grounding involves using ESD wrist straps and clothing to ensure that workers do not carry static charges when handling sensitive equipment. This helps minimize the potential hazards of electrostatic discharge to products. - ESD Protected Areas (EPAs):
ESD Protected Areas are designated zones where sensitive electronic components are produced, assembled, or tested. These areas should be equipped with effective grounding and protection measures to limit static accumulation and discharge. - Packaging:
Proper packaging materials can effectively protect electronic components from external static influences. For instance, using anti-static foams, bags, and containers can ensure that products are not damaged by electrostatic discharge during transportation and storage. - Labeling:
Clear labeling helps employees easily identify ESD Protected Areas and sensitive products. This includes using ESD symbols and warning labels to remind employees to follow ESD safety protocols, thereby increasing overall awareness of static protection. - Monitoring and Maintenance:
This involves routinely checking grounding resistance, the effectiveness of static protection devices, and the integrity of ESD Protected Areas to ensure that control measures consistently function as intended.
What are the three methods of controlling the ESD?
Understand how key factors influencing static electricity creation, we would know ESD can be effectively prevented by focusing on three key aspects:
- grounding all conductors (including humans)
- controlling insulating materials prone to generating static electricity,
- utilizing ESD protective packaging during product transportation and storage.
To provent ESD, we have this formula to follow:
ESD prevention =Human +Machine +Material+Method+Environment
● Human
-Use wrist straps, ESD shoes, ESD chairs, and appropriate clothing to minimize static generation from human contact.
To ensure the functionality of these personnel grounding devices, a reliable ESD combo tester is required.
Click here to find out how to choose the suitable ESD tester.
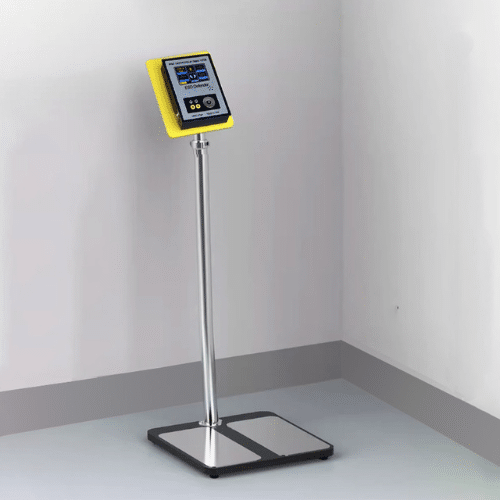
● Machine
-Ensure proper grounding of equipment to control static electricity buildup.
-Eliminate or shield electromagnetic interference and AC electric fields effectively.
● Material
-Use conductive materials
-Prefer materials that dissipate static electricity.
-Implement ESD flooring, table mats, and reduce the use of insulating materials
● Method
-Setup ESD protected area (EPA)
-Protect ESD-sensitive products or components from metal-to-metal contact.
-Shield non-ESD-safe items through Faraday or distance shielding.
-Eliminate static electricity through grounding and ionization.
● Environment
-Maintain temperature and humidity control.
-Consider localized ionizing fans.
-Provide ESD training to employees.
-Establish proper ESD management protocols.
The Principle of Grounding to Eliminate Static Electricity
Grounding is a common static electricity countermeasure used in both work and daily life. For example, at self-service gas stations, static elimination plates are directly grounded. When a person touches these plates, the static electricity on their body is discharged into the earth through the grounding. This effectively prevents accidents caused by static discharge sparks igniting vaporized gasoline.
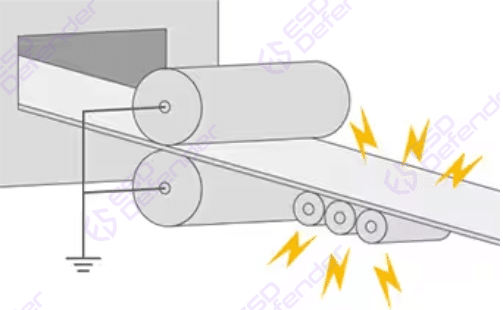
The same principle is also applied to production equipment and human. By simply grounding the equipment and human, static electricity can be eliminated.
Grounding the roller dissipates static electricity.
However, the propensity for static electricity generation varies across different material types. For more details, please refer to the section on The Electrostatic Properties of Different Materials.
Challenges of designing ESD control procedure
When designing an electrostatic discharge (ESD) control program, the following challenges are often encountered:
- Risk Identification and Assessment: Identifying and evaluating static electricity risks in various environments and equipment.
- Training and Awareness: Ensuring all personnel understand ESD risks and necessary protection measures.
- Material and Equipment Selection: Choosing appropriate ESD protective materials and devices to ensure effectiveness.
- Environmental Control: Managing humidity and temperature to maintain effective ESD control.
- Continuous Monitoring and Improvement: Establishing mechanisms for ongoing evaluation and enhancement of ESD control measures.